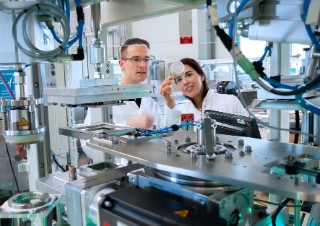
In the future, plastic packaging must be both resource-efficient and recyclable. To this end, Fraunhofer IVV is collaborating with partners to develop AI-based packaging solutions. These tools have been designed to optimise the life cycle assessment, design and material of packaging. All information is shared via a digital data room. This enables recyclates to be used more efficiently and packaging to be designed in a more sustainable way.
more info