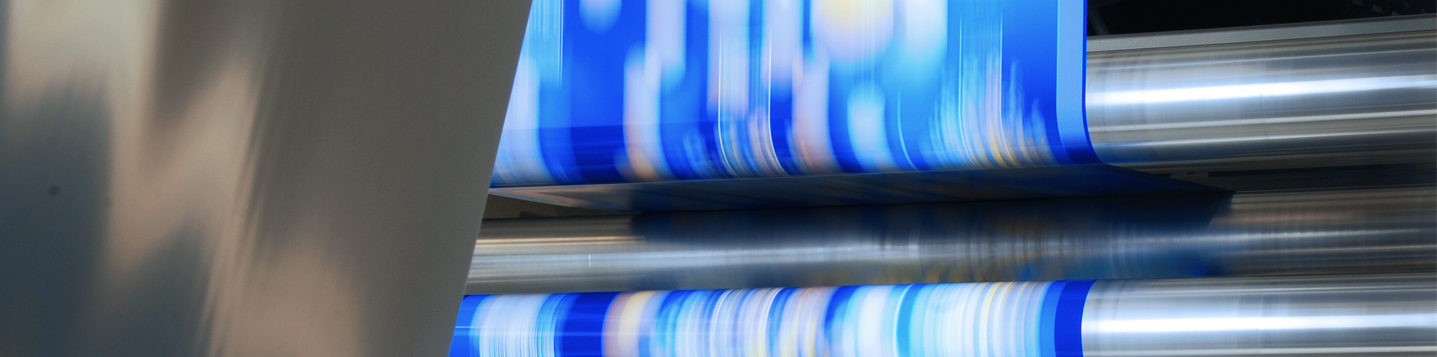
In addition to the manufacture of plastics, the further processing of plastics into packaging films and tubular bag packaging has huge industrial importance. Decisive factors for ensuring the required product quality are in particular the growing demand for lower usage of raw materials, greater flexibility when changing products, increased recyclability, and growing functional requirements on packaging. Very rigid films and highly sensitive films are an enormous challenge here.
Optimum machinability is also decisive in order to avoid quality fluctuations, defective packaging, product damage, and flatness problems.
We develop customized solutions to improve the quality of your products and stability of your processes. In some cases this is achieved by identifying and reducing sources of errors with the film transport and putting in place suitable corrective measures.
Fold formation, poor web transport, and the tearing of films are often the cause of errors with printed images, seam faults, and poor product quality. Good film transport on the other hand ensures the efficiency of the process and favorable use of resources. The machinability is determined by the film flatness, stiffness, and friction properties.
Our web transport test rig enables you to test the quality of your films and set process windows. The mobile oWTP scanner can be integrated into your plant to constantly monitor the film tension and flatness.
We can assist you with:
The filling of tubular bags is worldwide one of the most common packaging technologies. Although this involves particularly high requirements and complex interactions between the product, the packaging, and the machinery relatively little research is being conducted in this area. Even with the most modern machinery, common everyday challenges include sticking, abrasion, contaminated seams, errors with printed images, and poor web transport.
We can assist you with the optimization of your forming-filling-sealing processes and find a suitable processing window for your films. Utilize the many options for evaluating quality-related factors, from the web transport right through to the formed bag – if necessary using your own forming collars or other machine components.
Digitalization and adaptive processes are becoming ever more important for packaging technologies such as the filling of tubular bags. With our support, complex data sets can be recorded, evaluated, and processed. We can advise you - regardless of whether you use self-regulating systems or operator assistance systems.
Do you want to optimize your existing plant or commission a new plant? A prerequisite for this is always detailed analysis, to identify shortcomings and opportunities for optimization.
A system developed by us allows precise analysis of your plant. This consists of portable devices, optical counters, and cameras. Faults and their causes can be localized and traced. Throughout the analysis procedure your production plant can continue in full operation. Utilizing our technical knowledge and experience we assess any shortcomings, identify interrelationships, and propose solutions.
Our offer:
Many modern methods and scientifically established processes for material characterization have one thing in common: They do not represent real processes closely enough.
By working with us discover the important difference between friction coefficients under standard conditions and the friction coefficients under the actual processing conditions used for your films. Use our high speed friction measuring device to determine the industrially relevant measurement range and use these data in the film specification to improve film machinability.
The new method for biaxial film stretching allows totally homogeneous stretching without tears or ruptures for the development and improvement of new films for thermoformed products. Stretch your films using a clamping system made of elastic grippers. Optimum machinability is also important here.
The dynamic coefficient of friction is of great importance for evaluating the machinability of flexible packaging materials. Previous studies have shown that this depends on the relative speed of the packaging material against the tool surface (i.e. the contact points between the packaging material and the machine). In practice, processing and packaging machines are often operated at very high speeds or cycle rates. However, according to current standards, corresponding test procedures are only carried out at low speeds.
In order to counteract this discrepancy and to take into account the real events in the machine, we have developed a new test method as part of the WIPANO research project ("Development and standardization of a practical test method for determining the real coefficient of friction under processing-relevant speeds on packaging materials - HighSpeedFriction") and converted it into a standard (VDMA standard sheet).
For this purpose, a demonstrator was developed based on the principle of the Euler-Eytelwein formula for characterizing rope friction. The test method has been modified so that the packing material is pulled over a tool and no longer - as was previously the case - a carriage is moved over the packing material. This allows real load conditions from an industrial machine to be reproduced on a laboratory scale. The measurements are taken directly from the roll of packaging material, which means that sample cuts are no longer necessary. This also enables endurance tests, for example to examine the service life of a coating. Furthermore, the tools can have any curvature and size and the influence of the tool material and surface, as well as the wrap angle, can also be investigated.
We are your partner for processing technology including support to meet new packaging and processing requirements, carrying out complex R&D projects, introduction of new technologies in the field of digitalization and big data, and suitable networking of competencies.
Convince yourself!