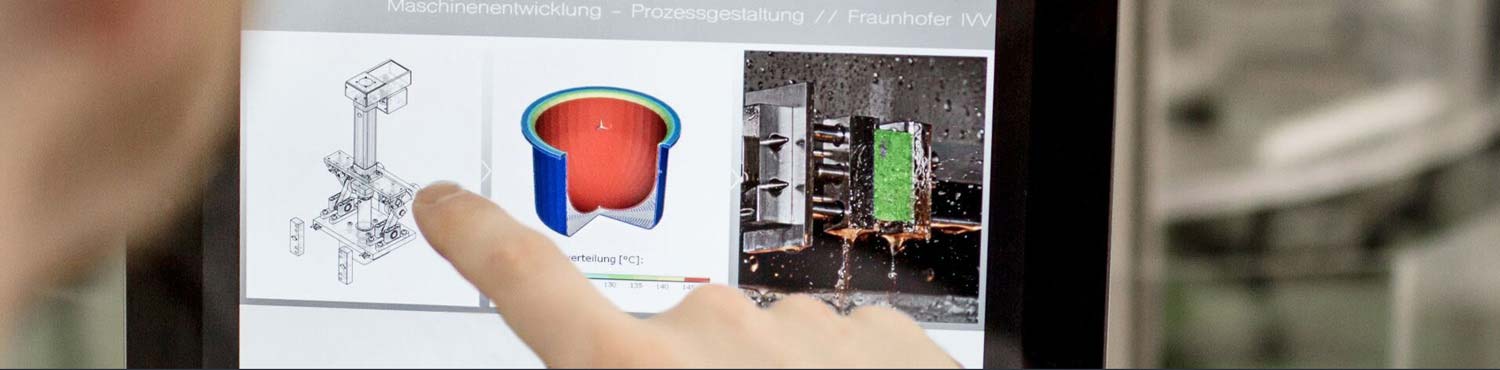
Product safety and process efficiency are the top priorities in the production of foods and pharmaceuticals. Realizing these objectives depends significantly on the effective collection and processing of process data. Process-related simulations identify the operating parameters for individual processing steps and enable, for example, optimal responses to variable packaging and product properties. The basis for this is seamless data exchange along the whole value-creation chain.
We develop solutions for the digitalization of food processing. With the aid of machine learning and simulations, adaptive systems are being developed in the area of film processing and cleaning. In order to support employees with the changing workplace of Industry 4.0, we are developing assistance systems to support, for example, the cognitive skills of machine operators.
We are helping customers optimize their processing chain and cleaning processes by analyzing their processes and the generated data, by identifying weak points, and by implementing suitable digitalization solutions.
The efficiency of processing machinery often depends on the experience of the machine operators. There is still, however, an inadequate exchange of knowledge and experience in most work environments. The self-learning assistance system for machine operators (SAM) combines machine learning with human experience in order to reduce production faults and increase the machine/plant efficiency.
Our VR-based trainings allow you to flexibly qualify your operating and technical personnel in a virtual production environment, away from the real production. The individually adaptable didactic concept makes it possible to convey learning content quickly and vividly and to make complex process interrelationships interactive to experience and learn.
For example, format changes or dealing with malfunction situations can be trained in a self-directed and risk-free manner. In addition, the process and experience knowledge available in the company can be saved and made available to the virtual training application. Machine parameterization can so be trained in a targeted manner.
Training in virtual reality ensures efficient onboarding of new operating personnel. At the same time, it enables an increase in the qualification level of permanent staff, so that operating errors due to a lack of instruction are reduced.
This minimizes disruptions and increases production efficiency.
Easy-to-understand visualizations of complex issues can increase understanding of processes and procedures, regardless of the employees' native language.
As a plant operator or manufacturer you benefit from professional analysis of the efficiency of your processing machinery. We are your expert, independent partner and help you increase the efficiency of your production processes.
We employ the most advanced analysis methods and possess in-depth knowledge of processes. As such we are able to identify potential technical and organization enhancements for your production operations.
The bringing together of interdisciplinary expertise from mechanical engineering, automation technology, and engineering psychology is enabling us to eliminate the gap between data availability and interface design. By analyzing the different operating tasks within the framework of domain requirements we are able to adapt the quantity, composition, and degree of detail of information on the HMI to the relevant task and information need. Knowledge from the area of psychology is also being used to optimize the display of information for human perception, cognition, and actions.
HMI concepts are usually developed by automation experts and design specialists. As a result, the availability of data and an optically attractive design are often the technical priorities for user interfaces. There is, however, a gap between the data and design which can be eliminated with a functional abstraction layer taking into account engineering psychology aspects.
Improved availability and coherence of the displayed information makes the system more transparent and easier to understand. This means less training for new operators. Tasks can be performed easily, rapidly, and error-free and the OEE positively influenced.
How can you find the digitization and assistance solution that is tailor-made to meet your needs among the broad and diversified offers? How can you increase your plant efficiency by means of smart support for your machine operators? How can you increase your employees’ satisfaction at the same time?
We provide objective advice, develop demand-based, customized digital solution strategies to meet the specific challenges of your production processes within the framework of a workshop with you and your machine operators, create a development roadmap, and if required, assist you with the implementation of the systems..
Fully equipping machines with modern digital measurement technology is not always economical, even for new plants, also because the actual benefits are often difficult to assess in advance. Large parts of the data remain in the machine instead of being put to beneficial use.
We address this practical problem with a modular solution for process data acquisition and digitalization. On the one hand, this consists of hardware and software modules for connecting relevant interfaces – from the analog power interface to Modbus TCP – to the uniform I4.0 data exchange format OPC UA or directly to AI-based tools.
On the other hand, the system solution seamlessly integrates the machine operator into the process data acquisition if required: Via a custom application, he supplements those quality-relevant process data in dialog with the system for which no measurement technology is installed.
Together, we develop your needs-based digitization system as well as future solutions for its beneficial use – from quality protocols for your customers to self-learning assistance systems to support plant operators to customized AI applications.
As a partner for the needs-based digitization of your processing operations, we offer you:
Augmented reality (AR) refers to the virtual extension of reality. Interaction and visualization elements (e.g. images, text, videos) are superimposed on live images of the real environment. Virtual reality (VR), on the other hand, immerses the user in a completely digital environment in which all elements are displayed virtually. Both AR and VR can be classified under the umbrella term Extended Reality.
Mixed Reality (MR) is the blending of virtual and physical reality. In other words, it represents the transitional area between the physical and the purely virtual world. Unlike virtual reality, virtual reality is enriched with real objects. This is achieved by VR glasses containing cameras that, for example, film the user's hands and embed them in the virtual environment (pass-through technology).
AR is used in food production primarily for remote maintenance or remote commissioning of machinery and equipment. The advantage is that the service engineer at the machine manufacturer sees the same thing as the person at the machine. In addition, useful information can be displayed directly in their field of vision and certain individual parts or assemblies can be highlighted. Communication is thus significantly simplified.
In addition, AR is being applied for operator assistance. For example, the Fraunhofer IVV has developed a virtual cleaning assistant that supports employees during the manual cleaning of machines and systems and documents the cleaning process. The cleaning personnel get an immediate visualization of the cleaning success in AR glasses and can, for example, re-clean any spray shadows that arise.
VR technology can be used very well for training operating personnel. In VR training via VR glasses, knowledge about a processing operation is imparted and the process steps are trained in a VR environment. The user can interact with the machine model, for example by changing setting parameters. The changes then have an effect on the process flow, as in reality, so that safe and efficient handling of the machine can be learned without interrupting the real production process.
High product safety can be continuously guaranteed despite the ever more complex processing and packaging requirements of food manufacturers.
To realize this objective we provide you with intelligent sealing tools that allow adaptive sealing and real-time evaluation of the packaging quality.
Adaptive cleaning systems guarantee effective, cost-saving cleaning with minimum use of resources and with continuous monitoring of the cleaning process.
We are experts in using numerical simulation as a tool to analyze, develop, and optimize materials, processes, and machinery. Specific for your application we analyze and identify the key steps, develop suitable material and process models, and use these for studies or optimizations.
You benefit from increased process understanding, cost and time savings, and improved process stability and efficiency.
We evaluate existing material models for their suitability for specific applications and determine parameters for simulating the real behavior. For this purpose we use established thermal and mechanical test methods such as DSC, uniaxial tensile testing, and compressive testing. We also continually develop new test methods and equipment, for example the biaxial tensile strength test rig, contamination sensors, and the bubble inflation test. We develop effective material models based on the selection and combination of suitable test methods and specially developed characterization methods. Our expertise in the area of material modeling ranges from rigid bodies to elastic, viscoplastic, and fluid materials. Our focus here is on the characterization of plastic films and sheets, plastic-based hybrid materials, and fluid flows.
The relevant components are modeled based on analysis of the process. We possess a variety of commercially available and open source numerical simulation programs that enable us to study thermal, structural, fluid mechanical, and coupled issues. Our longstanding expertise covers element selection and networking, model selection and contact definition, and definition of boundary conditions and loads.
Using the process model we are able to simulate your process and acquire detailed insight into temperature and flow fields and stress and deformation parameters. Experimental limitations due to opaque walls, high temperatures, and aggressive media become a thing of the past. The effects of changed material and process parameters and geometry details can be predicted, whilst reducing production times and costs. Based on this we identify optimal design and process parameters (for example for sealing and thermoforming), we maximize the cleaning effect (for example via geometrical changes), and we use our increased process understanding to develop improved, innovative processes and technologies.
At present the design of cleaning systems is largely based on empirical knowledge and on iterative modifications to prototypes. In order to simplify and accelerate this for the demanding process of spray cleaning, the simulation software ADVISIM3D was developed in a BMBF funded project. This software is a powerful optimization tool for designers of spray cleaning systems. Besides allowing the design and evaluation of static and dynamic spray cleaning systems (e.g. for tank cleaning), the user-friendly CAD tool allows prediction of the effect of complex cleaning systems in which the jet impact and the run-off fluid are taken into account as cleaning components . Utilize innovative CAD software for your design process. As a service we can perform simulations for you or can provide you with relevant training and can help you with the measurement and database integration of nozzles.
The software was launched in October 2020.
We offer simulation services for various objectives: