Developing a recycling process for the recovery of plastics from galvanization waste
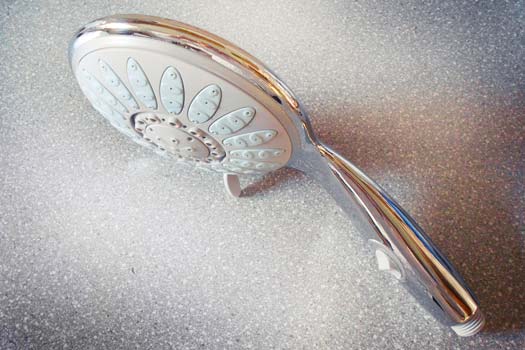
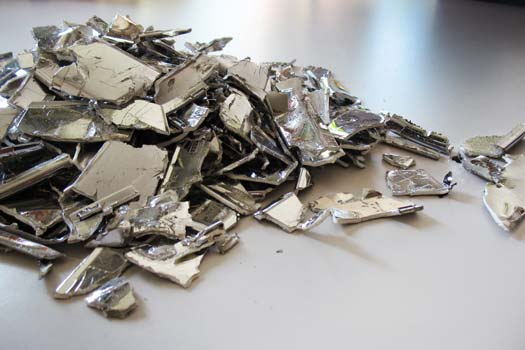
The aim of the FiltraSolv project is to develop a polymer recycling process and to recover high-quality plastic products from plastic-containing electroplated waste. The recycled plastic must be recovered in a quality that meets the high requirements for electroplating.
Recycling problem of galvanized plastics
Electroplating gives plastic components such as fittings, household appliances, door handles, and car parts a stylish, high-gloss appearance. The production of these electroplated plastic products has a reject rate of 10 to 30%. The rejected products cannot be reused in the production because the components of the electroplated layer would block the injection nozzles. Simultaneously, the purification of the wastewater produces large amounts of galvanic sludge that has to be disposed of as special waste.
If the raw material cycle could be closed via high-quality recycling of the electroplated plastic waste and work-up of the galvanic sludge, then high transport costs for disposal and costs for new plastics could be saved. Plastic producers could also reduce their CO2 emissions.
Reuse of galvanic waste through polymer swelling
The recycling process that is being developed and tested in this project is based on polymer swelling. Due to the low use of solvents it can implemented using conventional plastic processing machinery such as an extruder with melt filtration and vacuum degassing. Such a system would enable polymer swelling, filtration of electroplating metals, and solvent recovery in one line. Compared to hitherto solvent-based plastic recycling processes, the operating costs and investment costs for this new process would be considerably lower.
The process will first be developed and tested on a small scale in the laboratory. The process will then be carried out on a larger scale to test the stability of the process and to plan for industrial realization.
Project term: |
2011 to 2013 |
Project management |
Federal Foundation for the Environment DBU |