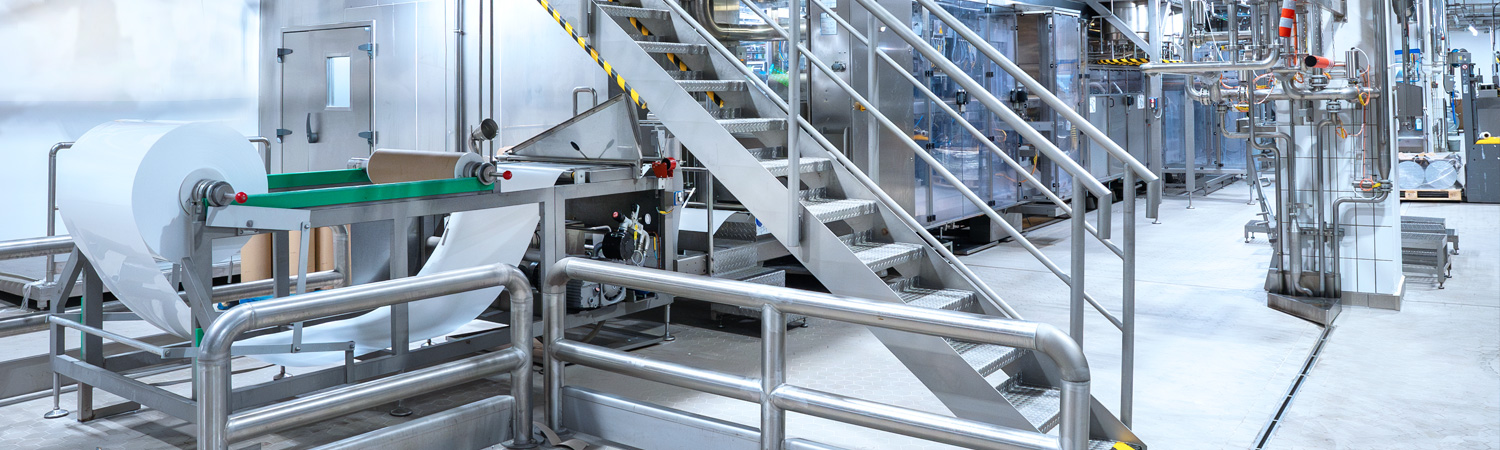
for packaging production
The competitiveness of companies in the food, cosmetics and pharmaceutical industries depends on the implementation of customer interests in products and their technical production. Inefficient development processes and production disruptions reduce profitability. This applies in particular to small and medium-sized companies in Germany. For over 20 years, we have been involved in research into packaging processes and have built up extensive expertise in the development and optimization of packaging processes.
Our focus is on packaging processes for film or paper applications on form-fill-seal machines, forming (e.g. thermoforming or deep-drawing processes), sealing and cutting. Our know-how, our laboratory and sensor equipment, as well as our many years of experience, enable us to determine the overall equipment effectiveness, identify production disruptions and develop and implement optimization proposals. In addition, we develop novel production and process concepts and test them in our pilot plants. Our network of various companies in the value chain – from material manufacturers, tool and machine manufacturers to producers – ensures that a process is developed from the initial idea to series production. Furthermore, we support our partners in testing their own developments in our real-world laboratory.
We contribute our expertise to joint projects with our partners with the aim of developing specific and concrete solutions for their applications.
Are you looking for ways to increase the efficiency of your production processes?
In our research projects, we work with our partners to optimize processing and packaging processes based on specific requirements. We focus particularly on the interactions between material, machine, and packaged goods. To develop suitable solutions, we analyze technological implementation, material selection, machine parameterization, and operator interaction.
Based on our expertise and extensive experience, we identify the interactions between influencing factors and targeted quality criteria for your specific application. For various promising approaches—material selection, tool design, technology, and machine parameterization—we assess the optimization potential. Our flexible laboratory test stands allow us to determine the relevant processing ranges of material-process-tool combinations for forming, sealing, cutting, and film handling. The identified process windows, interactions, and optimizations help improve the cost-effectiveness of your processes. Depending on your specific needs, we can also introduce alternative packaging technologies. Additionally, we support you in determining suitable machine settings or transferring existing machine parameters to alternative processing and packaging machines.
We support you in:
Are recurring malfunctions in your processing and packaging machines, along with increased waste, reducing your planning reliability and driving up production costs?
We identify the causes of production disruptions, propose solutions for their elimination, and support their implementation.
To analyze and resolve issues, we combine our extensive measurement technology with expertise gained from numerous research and industry projects. Our data acquisition tool EV²E enables us to precisely capture the impact of disturbances on machine availability. Leveraging the knowledge of our experts, we conduct in-depth interaction analyses of production conditions to determine the root cause of disruptions. Additionally, we utilize various temperature, force, and pressure sensors to measure critical operating conditions in your facilities. Based on this data, we simulate scenarios numerically or experimentally in our technical center to develop solutions for complex disturbances or validate them in advance. This allows us to identify critical process steps and assess the impact of process and material fluctuations on production stability—while ensuring minimal disruption to your ongoing operations.
We support you with:
Do you need to expand your process or are you looking for a suitable packaging process for your application?
In various projects, we assist our customers in solving their challenges. For example, we have developed a functional laboratory pouch, a forming process for conformable electronics, sealing processes for paper applications, and much more. We are happy to support you in developing a process solution tailored to your application.
Based on your objectives, we structure the development process into clear project steps. We support you from the initial idea through Technology Readiness Level (TRL) 1 to full-scale production implementation (TRL 8). Through our research projects, we stay up to date with the latest scientific and technological advancements and integrate this knowledge with our development expertise.
We employ various experimental and numerical methods to drive development efficiently. Our test stands allow us to replicate industrial conditions and validate developments at a laboratory scale. This enables efficient analysis of different scenarios in an industrial setting and facilitates data-driven decision-making using advanced measurement technology. Additionally, we can produce small batches for testing purposes directly in our laboratory.
Through our extensive network, we maintain strong connections with material and technology suppliers, machine manufacturers, and producers. This helps us—and you—identify suitable partners to support the realization of your ideas. Furthermore, we assist in scaling development from the laboratory to an industrial environment. With our expertise, you can build on a solid foundation of knowledge and fully leverage the potential of your project.
We support you with:
Are you looking for a way to test and refine your solutions for packaging machines and processes in small production runs?
We offer a comprehensive technical center equipped with innovative laboratory test stands and advanced industrial systems. These allow you to validate developments in an industry-relevant environment and identify potential early on.
Our real-world laboratory features a horizontal and vertical form-fill-seal machine, a model system for thermoformed packaging (MotiV), and various sealing systems utilizing different technologies, including heat contact, ultrasonic, impulse, induction, and high-frequency sealing. Additionally, we provide a range of temperature, force, and pressure sensors to monitor the process. Our measurement technology also enables precise evaluation of the resulting packaging quality.
A key advantage of our real-world laboratory is its ability to systematically replicate industrial scenarios—such as contamination on films, wrinkle formation, or product residues—allowing for a structured analysis of functionality. Utilizing our technical center enhances the efficiency of your development process, as you can initially disregard regulatory constraints from the food, cosmetics, and pharmaceutical industries.
We support you with:
Are you reaching the limits of experimental testing? Would you like to identify the optimal development solution for your packaging, processing methods, and machinery at an early stage or accelerate the development process?
We have extensive experience in simulating the interaction between materials, machinery, and processing methods—for example, in thermoforming, sealing, and deep drawing. Working both independently and in collaboration with partners from industry and academia, we continuously refine our simulation methods, overcome existing limitations, and redefine feasibility boundaries.
To achieve this, we use commercial simulation software such as ANSYS and LS-DYNA while also contributing to the development of new software solutions for processing plastics and paper. This gives us expertise in both established and emerging approaches, along with a broad network of research and industry partners.
With our laboratory testing equipment, we can characterize materials based on industry-relevant factors such as temperature and humidity. The well-equipped, high-performance pilot plant at Fraunhofer IVV, featuring various test rigs and industry-relevant machines in combination with high-resolution measurement technology—such as high-speed cameras, infrared cameras, and more—enables detailed validation of processes and process steps. Additionally, our experienced engineers develop customized test rigs tailored to specific applications.
This allows us to create simulation models and methods specifically adapted to your needs. Based on these models and study results, you can make informed and efficient decisions, avoiding time-consuming trial-and-error approaches in development.
We support you with