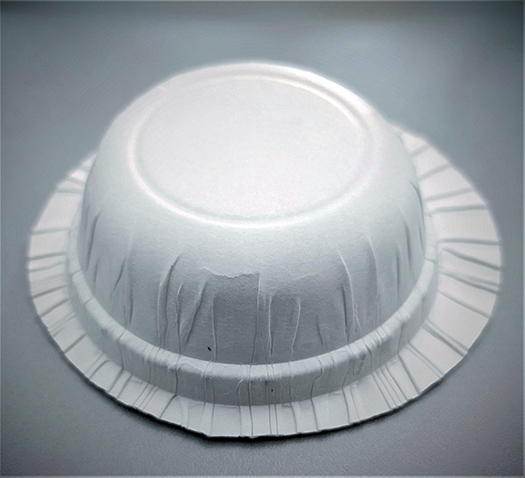
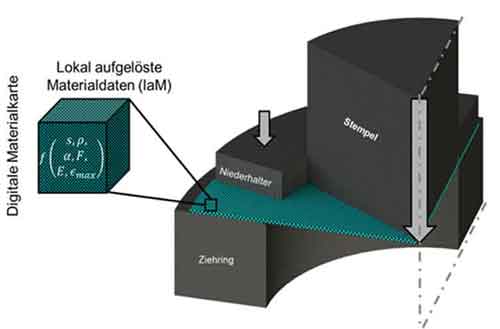
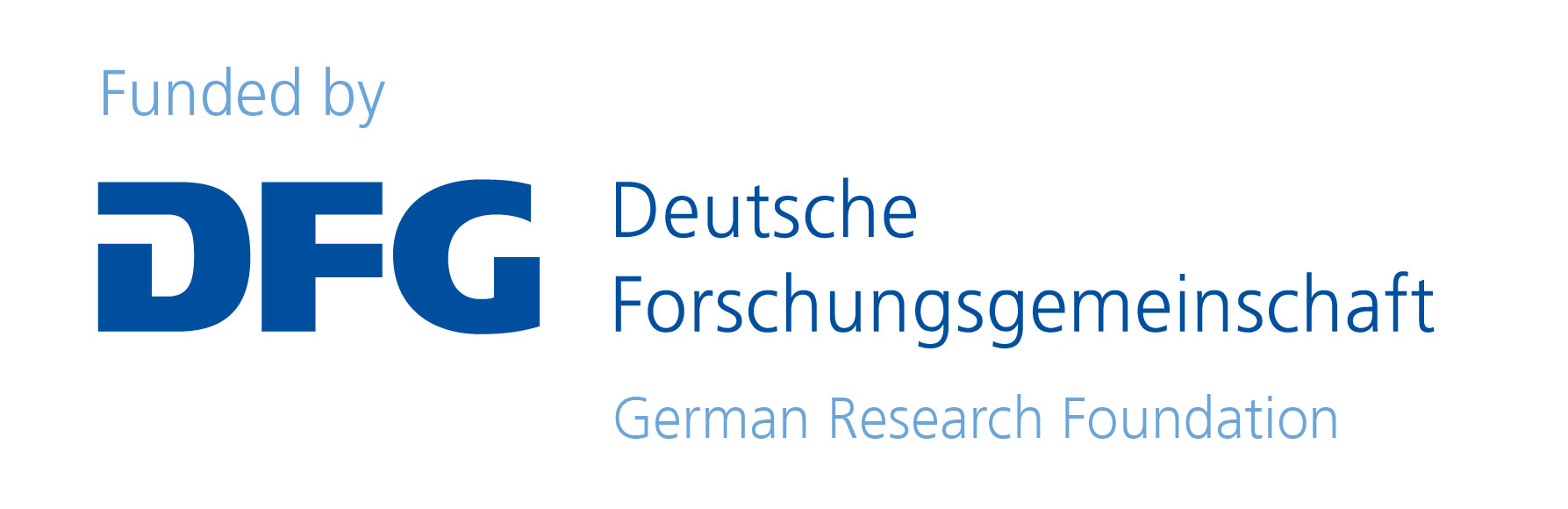
Greater visibility of the invisible
In moving toward a resilient, self-reliant circular economy, there is still a real need for sustainable alternative solutions for plastic packaging. An important approach here is the use of fiber-based packaging materials, as paper and cardboard are seen as an ecologically advantageous alternative compared to other packaging materials. However, these packaging materials have lower stretching capacity and high variations in forming quality. Inhomogeneous material properties hinder the production of complex packaging designs, and the lack of non-destructive measurement and quantification of material properties to date makes targeted process control difficult.
As part of the German Research Foundation’s (DFG) SimBoard project, we are working with the Technical University (TU) of Darmstadt to develop a measurement method for determining the paper structure and an associated method for numerically mapping the inhomogeneous material properties in FEM simulations in order to make them “visible” for analyses. The objectives of the research project are to increase process stability and to expand the fields of application in paper forming.
Greater process stability in the production of sustainable packaging
To achieve the project objectives, the relationships between the inhomogeneous physical and structural material properties and the resulting mechanical material properties relevant for processing must be known. To this end, the research project is investigating the measurability of these identified properties to identify possible correlations.
Simple and rapid measurement techniques are being used to evaluate the relationship between the relevant state of inhomogeneity of the material and the associated effect on the forming process. The material behavior resulting from these interactions is then mapped in a numerical model.
The aim here is to develop a method for numerically representing the randomly distributed material data. Crack initiation (damage) during the forming process is also shown. Finally, recommendations for increased process stability in paper forming and implementing new forming geometries and dimensions will be able to be derived.
Quality assurance and new application and design possibilities
Through the targeted detection of existing fluctuations in the paper structure and the resulting early initiation of suitable measures for the adaptation and optimization of the forming process, the method for numerically mapping the material inhomogeneity of fiber-based packaging materials allows quality-assured formed part production and the development of entirely new packaging designs.
In addition, these investigations provide a substantial gain in knowledge with regard to the forming mechanisms of paper that actually result from different material structures. On this basis, appropriate recommendations can be derived for paper production in line with forming and quality requirements. This results in a reduction in rejects, an increase in process stability and an expanded range of applications for paper forming.
More advantages at a glance:
- Targeted paper development through quantifiable and measurable variations in material properties
- Cost- and time-efficient error root cause analysis
- Faster market maturity and market access for new materials and packaging
- Reduced production downtimes and rejects, as well as conservation of resources by reducing the use of materials
If you have any questions or would like more information about our research project, please feel free to get in touch!
Project information SimBoard
Project duration | January 1, 2021 to December 31, 2023 |
Funding number | TU Darmstadt (Institute for Production Engineering and Forming Machines) |
Project sponsor/Grant authority | German Research Foundation (DFG) |