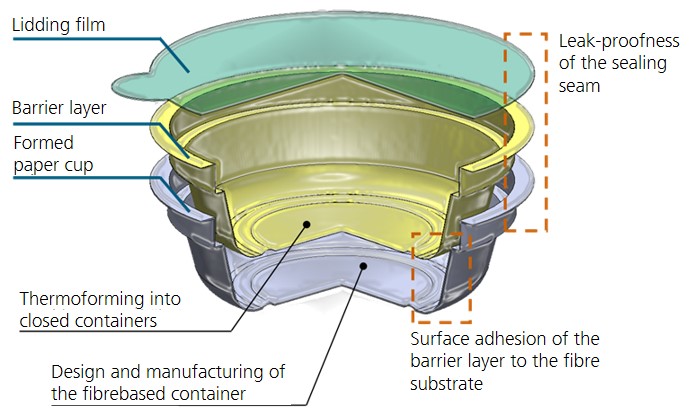
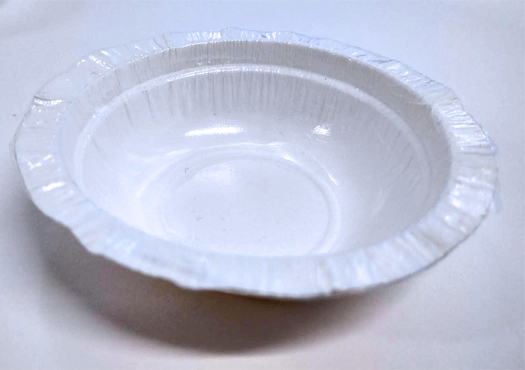

Protection of sensitive products with minimal use of plastics and full recyclability
To achieve a circular economy, the "Pack4Sense" project is dedicated towards the development of a packaging concept, which ensures easy separability of the packaging components while fulfilling the barrier requirements of sensitive food products with minimal usage of plastic.
Fiber-based materials such as paper and cardboard are increasingly used as a substitute for plastics made of fossil resources. Besides the advantage that renewable raw materials are used for the production, recycling infrastructures are also established worldwide.
Due to the fact that paper and cardboard have limited barrier properties, for example against oxygen, plastic barriers are still commonly used. However, the barrier is laminated, which makes it difficult to separate the composite. As a result, full recyclability cannot be achieved because the components cannot be added to the intended recycling chain.
In order to solve this problem, a new approach has been developed which enables the coating of paper mouldings by forming a thin film into the moulding using the thermoforming process. This allows the production of packagings with a high fiber proportion and reliable barrier properties, which can be disassembled into their individual parts after usage.
High quality barrier layers and secure sealing seams for fiber-based packaging
The forming methods used are based on the compression of excess material, which results in the characteristic wrinkling of the moulded part. As a result, the sealing edge causes leaky sealing seams, because the unevenness cannot be completely sealed with the melted material. When using the thermoforming process for coating, the film lays over the uneven sealing edge and allows a tight seal of the packaged goods.
Another advantage is the prevention of unwanted material damage. When forming coated fibre materials, the abrasive contact between the packaging material and the forming tools can result in significant damage to the barrier layer. When the film is formed separately, the applied process forces and tool contacts are significantly lower, which prevents damage to the barrier layer.
The forming of the thin films results in process-related challenges, which are mainly due to the specific thermomechanical properties of the thin films. The Fraunhofer IVV Dresden is developing solutions to drastically improve the forming of thin films in the thermoforming process.
Individual design of the shape and barrier properties of food packaging
The project results have shown that the thermoforming process can be used to apply a thin barrier layer to the inside of fibre-based packaging. This results in a new method for reducing plastic waste, which complements the three-dimensional paper forming process. Good barrier properties and stable process designs can be achieved while maintaining sustainability, as separation of the components is possible after usage.
Do you have any questions or require further information about this project? Please get in touch with us!
EIT Food is supported by the European Union
Project term | January 1, 2021 to December 31, 2021 |
Project partner |
Colruyt Group [Belgium], Strauss Group [Israel]; Syntegon Technology GmbH [Germany], University of Reading [UK] |
Project management /funding: |
European Institute for Innovation and Technology EIT Food |