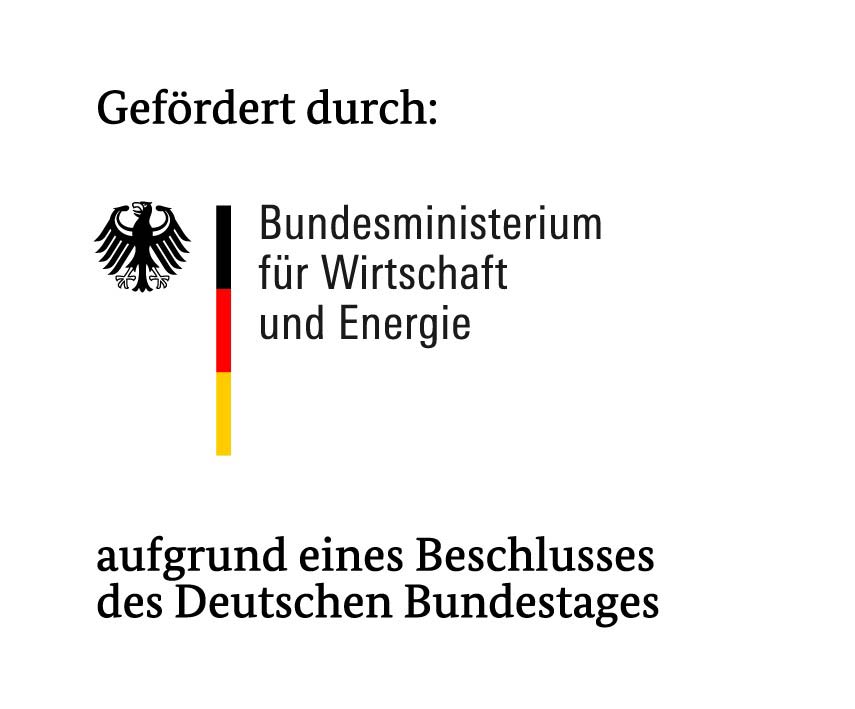
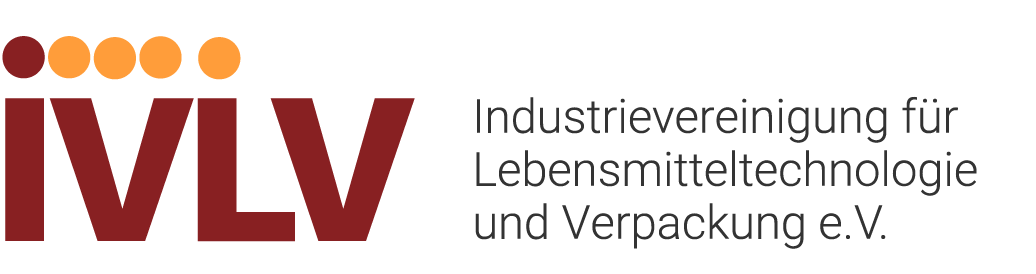
Forming air impact technology for customized material distribution
The Forming Processes group at Fraunhofer IVV in Dresden is using a precisely directed flow of forming air to try and resolve the issue of technology-related variations in the material thickness of thermoformed parts.
Depending on the application and function of thermoformed parts, specific quality requirements must be met in terms of their geometry and resistance to compression. If the material thickness is uneven, more material is required in order to meet mechanical stability requirements.
The use of forming air impact technology makes it possible to achieve a defined distribution and thickness of material. The consequence of this is a better use of material, improved quality parameters and enhanced efficiency of the thermoforming process.
In order to achieve significant reduction in the time and cost to design this technology in line with required product specifications, the Fraunhofer IVV group is now developing a parameterization tool. This also addresses shortcomings with other technologies currently used to enable a customized control of the forming process. These technologies are maintenance-intensive, costly, difficult to parametrize, and often lead to a progressive deterioration of product quality over the course of the manufacturing process.
Parameterization of the airflow enables controlled thermoforming
Forming air impact technology subjects the substrate or semi-finished product to both a mechanical and thermal impact. First of all, the product is homogeneously heated and is then formed via a precisely directed flow of forming air from a nozzle system (forming air impact).
In order to develop a parameterization tool for the optimization of process design, a number of approaches were evaluated, including the Fluid Structure Interaction (FSI) model and machine learning. We also analyzed their potential application for the purposes of tool parameterization in thermoforming.
The focus of the project is to develop a concept for an industrial use of forming air impact technology in a controllable forming process using compressed air. Here, the key challenges lie in not only the dynamic process itself but also the interaction between fluid flow and the forming of the plastic semi-finished product.
What can the process be used for?
Forming air impact technology has huge potential for the manufacture of packaging. By focusing on the interaction between the cooling and forming of plastics by means of a fluid flow and the development of a parametrization tool, the project also creates numerous other openings in, for example, medical technology, the automotive industry, and the field of smart molded structures (SME).
Do you have any questions or require further information about this project? Then please get in touch with us!
Project term |
April 1, 2019 to March 31, 2021 |
Project partner |
Friedrich-Alexander-Universität Erlangen-Nuernberg, Department of Chemical and Biological Engineering, Chair of Fluid Mechanics |
Project management/funding | German Federation of Industrial Research Associations AiF (through the Research Association of the German Food Industry FEI / Federal Ministry for Economic Affairs and Energy BMWi) |