Innovative technology for recycling PET waste into new bottles
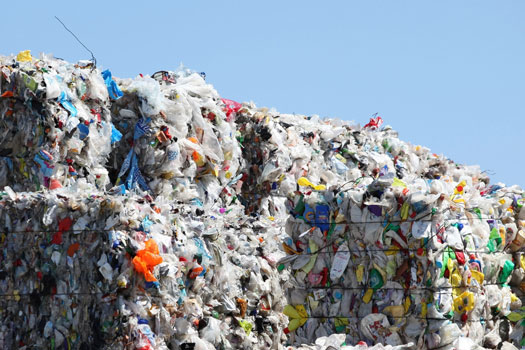
The Fraunhofer IVV has carried out a research project, funded by the BMBF, to develop a new recycling process. Post-consumer, mixed PET waste from DSD collection (the kerb-side collection system in Germany) has been able to be recycled such that the recyclate can again be used for bottle manufacture. Mechanical recycling of even mixed PET waste to produce materials that can be used for new bottles is hence possible.
High-quality PET recycling requires further development of recycling technologies
The increasing use of PET bottles means that the quantity of PET waste in Germany is continuously growing. In 2002, 70,000 tonnes of PET was collected via the DSD system. The introduction of a mandatory deposit drastically reduced the quantities of PET collected via the DSD system. Simultaneously, the complexity of the waste increased markedly. The fraction of PET bottle waste from the non-food sector collected via the DSD system is currently 15% and in addition there is a lot of packaging materials (films, trays and blister packs). The total quantity of PET waste that is collected is growing annually by about 15%. With the growing use of multi-layer packaging materials (including coatings and new additives for improved oxygen barriers) there is, in addition to the PET, an increasing amount of other plastics entering the recycling loop. As a result, the composition of the PET is changing. This requires further development work to be undertaken on PET recycling.
Innovative solvent-based PET recycling
The separation of the PET-containing, contaminated, different colored plastic waste from the DSD collection into type-pure fractions using conventional float-sink methods or methods based on the optical and electrostatic properties of the materials has proved unsatisfactory. Only a customized separation process, which removes the contaminants from the plastic matrix by purifying the polymers at the molecular level, is able to produce the required recyclate properties.
In the innovative process we have designed, a selective solvent dissolves the target PET into its macromolecules, but does not attack the macromolecules. Inert and dissolved contaminants are then separated from the recovered polymer solution by mechanical and chemical-physical methods. The next stage of the process involves adding a selective precipitating agent and precipitation of the PET by altering the temperature. The research team has tested many solvents for selective dissolution of the PET and based on this work has developed a special solvent formulation (not subject to declaration obligations under EU regulations) which from a commercial perspective also guarantees viable processing parameters. Aromatic and halogenated solvents were not considered due to their toxicity and classification as hazard materials. The solvents were recycled, mostly by mechanical means, and this has a favorable impact on the energy usage. The quality of the separation of the solvent and precipitating agent has a key influence on the quality of the product and the effectiveness of the process.
High-quality PET recyclate and scalability for industrial applications
The process was first of all developed on a laboratory scale and then scaled up via an intermediate stage to a small pilot-plant. This procedure guarantees that the process can be transferred to industrial scale and provides key scale-up parameters.
The evaluation of the rheological and optical quality of the recyclate materials was carried out in collaboration with British experts and DuPont. The results demonstrated the high quality of the recycled products. Based on comprehensive evaluation of the process, which
took into account technical, environmental and economic aspects to an equal degree, the project group specified the technical data for an industrial plant in detailed plans for realization of the process in practice.
Project term: |
|
Project management |
Federal Ministry of Education and Research (BMBF) |