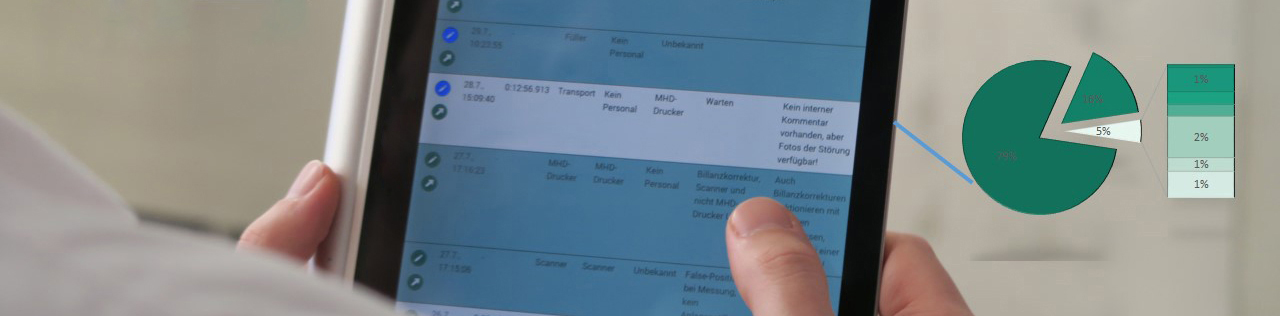
We offer plant operators and plant manufacturers assistance with efficiency analyses and improving the efficiency of production processes. Our state-of-the-art analytical methods and process know-how enable us to identify potential technical and organization enhancements for your production operations.
Detailed analysis is a prerequisite for plant acceptance and customized plant optimization. This allows the identification of shortcomings and opportunities for optimization. A system developed by us allows precise analysis to be performed. This system comprises portable devices, optical counters, and cameras and enables us to localize and evaluate faults and their causes. Utilizing our technical knowledge and experience we assess any faults or shortcomings, identify interrelationships, and propose solutions. Throughout the analysis your production plant can continue full operation. Detailed diagnoses using state-of-the-art analytical techniques enable faults to be clearly assigned to either the production operation or the machine manufacturer. Our analyses provide objective data in the event of conflict between plant manufactures and operators. The data can be used for constructive discussions between the parties and facilitate fast plant handover. The analysis of existing plants enables the identification of key components and procedures. This then presents scope for significantly increasing plant efficiency and lowering production costs. We provide on-site training to allow you yourself to carry out analyses and discover the potential of your production processes.
Based on your technical requirements and on-site discussions we identify what plant components are of particular importance for you, what performance parameters must be realized and where, and what products should be produced and in what quantity, etc.. For plant inspection we define, in consultation with you, the system limits and systematically split up the plant into sections. We then observe and analyze the performance of your plant in operation. A meaningful analysis or acceptance test requires an observation time of ca. 48-72 hours. During this procedure your production can continue undisrupted. After we evaluate the acquired data you are given a detailed report and presentation. We discuss and appraise with you strategies for improvement.