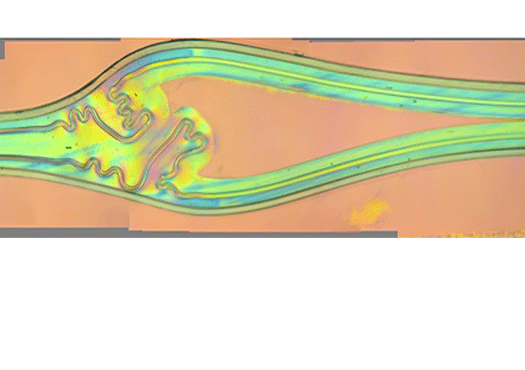

Influence of the sealing seam geometry on the sealing seam strength of film packaging
The reliable sealing tightness of the sealing seams and consumer-friendly easy-opening behavior are both important quality criteria for peelable packaging in the food, pharmaceutical and cosmetics industries. In heat contact sealing, high sealing pressures result in a strong melt flow of the sealing material, resulting in the formation of pronounced sealing beads. These, in turn, can severely limit the functionality of packaging — through the loss of peelability, for example.
To date, however, neither the influence of the sealing pressure on the sealing seam geometry nor the influence of the sealing seam geometry on the sealing seam strength have been methodically investigated.
Simulation-supported strength and failure analysis of sealing seams
In the AiF project “Seal Strength Simulation”, a method has been developed that makes it possible to numerically analyze factors such as sealing seam geometry and material properties of the film composite on the sealing seam strength.
To achieve this, the influence of the film structure and the sealing parameters on the sealing seam design and the seam strength was first investigated experimentally. In the second step, a simulation method and a simulation model for predicting the strength behavior of sealing seams were developed on this basis.
When developing the simulation method, a fracture model for describing crack propagation was derived from the analysis of the fracture mechanism and the seam strength in the experimental part of the project. The geometry of the sealing seam design and the layer structure of the sealed films were then transferred to CAD data using microscope images. The sealing seam geometry and the information about the layer structure are linked with the aid of the CAD data.
For the simulation model, the parameters and characteristics developed in the simulation method were then transferred to a commercial finite element (FE) software package, the sealing seam geometry and the individual layers were uniformly meshed, and the seam strength test was simulated in the form of the T-peel test (DIN 55529).
Both the experimental part and the FE simulation have confirmed that the sealing seam design, with the associated beads and notches, is a relevant influencing factor on the separating and tearing force for peelable film composites. It must therefore be taken into account when designing the process and material for the packaging.
Optimization of the development process for film systems and packaging
Unknown influencing variables of the individual film composite layers, such as the backing material or the barrier layers, on the expected sealing seam strength can be predicted using the simulation model developed in the project. The freely parameterizable simulation model makes it easy to adapt the geometry, material properties and sealing seam design. At the same time, the numerically calculated results can be used to derive optimized material properties, layer structures and sealing seam geometries for quality-assured sealing seam strength.
The ability to numerically calculate the influence of the sealing seam design, the layer structure and the material properties of the individual films on the sealing seam strength allows companies to reduce resource-intensive adjustments to their film systems in the development process. Unknown influencing variables of individual film composite layers, such as the backing material or barrier layers, on the expected sealing seam strength can be predicted using the simulation model developed in the project. The freely parameterizable simulation model makes it easy to adapt the geometry, material properties and sealing seam design. Using the numerically calculated results, optimized material properties, layer structures and sealing seam geometries can be determined for quality-assured sealing seam strength.
If you have any questions or would like more information about our research project, please feel free to get in touch!
The IGF research project “Seal Strength Simulation” (IGF project no. 20657 N) of the Industry Association for Food Technology and Packaging (IVLV e. V.) was funded by the German Federal Ministry for Economic Affairs and Climate Action (BMWK), via the German Federation of Industrial Research Associations (AiF) within the framework of the program for promoting collective industrial research (IGF) on the basis of a resolution of the German Federal Parliament (Bundestag).
Seal Strength Simulation project information
Project duration | April 1, 2019 to December 31, 2021 |
Funding number | 20657 N |
Project sponsor/Grant authority | German Federation of Industrial Research Associations (AiF) via the Industry Association for Food Technology and Packaging — IVLV e. V. / German Federal Ministry for Economic Affairs and Climate Action (BMWK) |