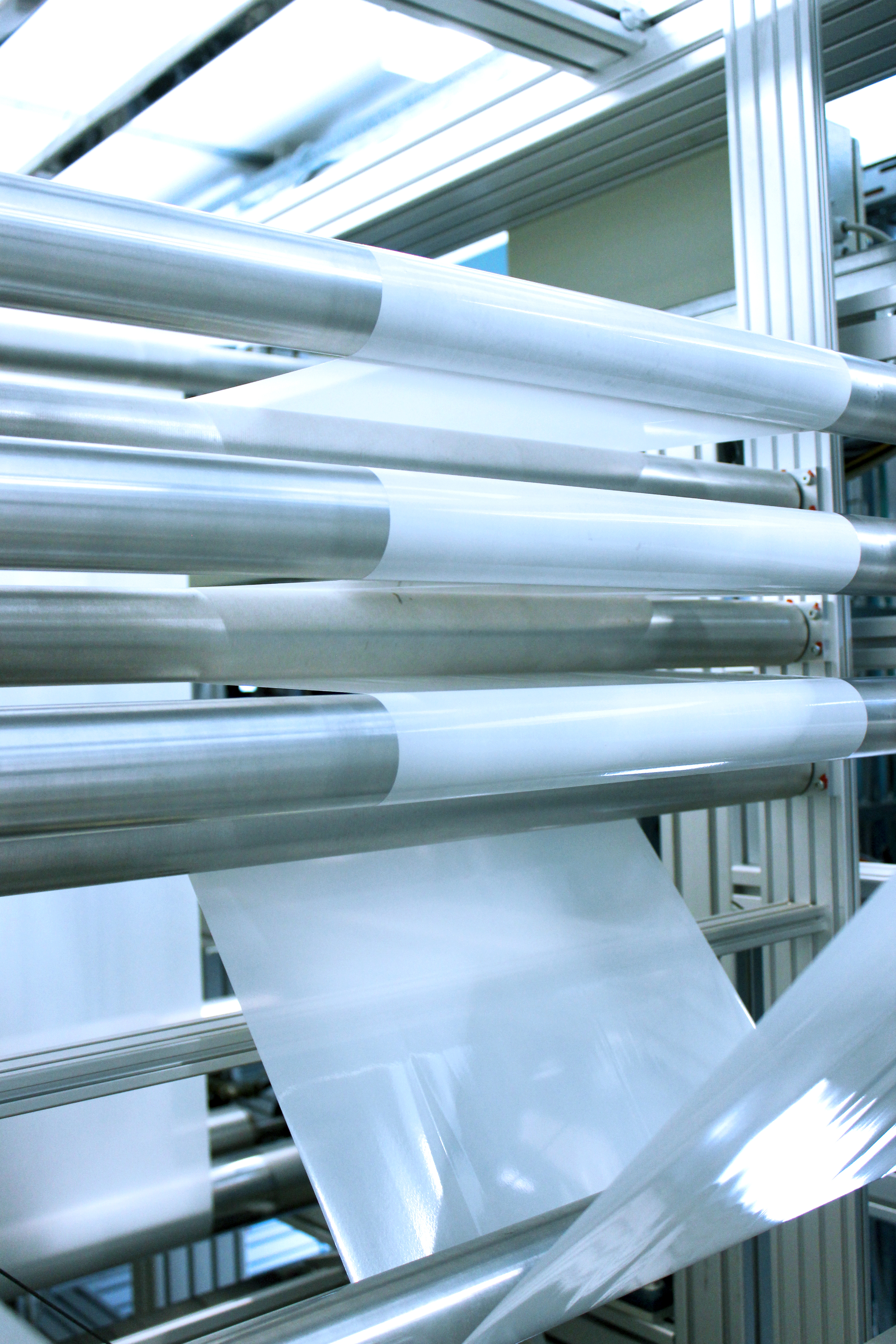
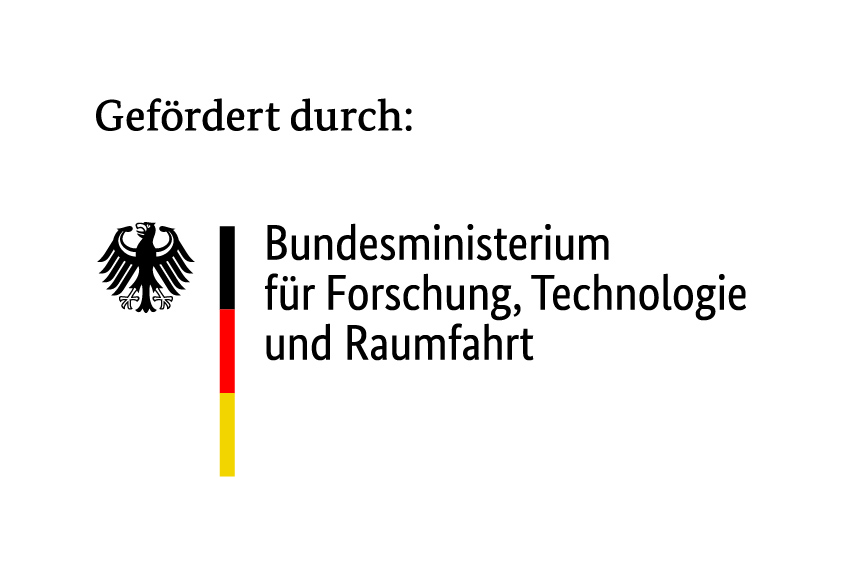
Gestiegene Anforderungen beim Wärmekontaktsiegeln von Monomaterialien
Das Verschließen flexibler Verpackungen für Lebensmittel, Kosmetik-, Pharma- und technische Produkte erfolgt überwiegend durch Wärmekontaktsiegeln. Die Gewährleistung der Produktsicherheit stellt dabei höchste Anforderungen an die Qualität der Siegelnähte, insbesondere deren Dichtigkeit und Verschmutzungsfreiheit. Unzureichend eingestellte Siegelparameter, Lufteinschlüsse, Falten und Kontaminationen im Nahtbereich können jedoch zu nicht qualitätsgerechten Siegelnähten im Produktionsprozess führen.
Die im Sinne einer Kreislaufwirtschaft zunehmende Substitution mehrlagiger Verbundfolien durch recyclingfähige Monofolienverbünde führt aufgrund deren enger Verarbeitugsfenster verstärkt zu Problemen beim Wärmekontaktsiegeln. Dies erhöht die Notwendigkeit einer lückenlosen Nahtinspektion in der Produktion, um den Transport fehlerhafter Produkte zum Verbraucher zu verhindern und Ausschuss durch eine frühzeitige Detektion der Fehlstellen bereits beim Produzenten zu reduzieren.
Bisher eingesetzte Verfahren zur Nahtinspektion genügen diesen Anforderungen nicht, da sie meist nur offline für Stichproben geeignet sind und die Verpackung dabei zerstört wird. Eingesetzte Inline-Verfahren, wie z. B. CO2-Prüfgastests, erreichen wiederum nicht die erforderliche Geschwindigkeit für eine lückenlose Prüfung aller produzierten Packungen. Darüber hinaus ermöglichen die meisten Verfahren keine Lokalisierung und Klassifikation der Fehlstellen anhand von Merkmalen zur Bewertung kritischer Defekte.
Prüfsystem zur zeitnahen, durchgängigen Inline-Nahtkontrolle im laufenden Prozess
Ziel dieses Forschungsvorhabens ist es daher, ein neuartiges Prüfsystem zur 100% durchgängigen Inline-Kontrolle von Siegelnähten zu entwickeln. Als zielführende Methode zur Fehlerdetektion wird die optische Kohärenztomographie (OCT) angewendet die es ermöglicht, mittels dreidimensionaler Fügenahtbilder Fehlstellen zu erkennen und zu quantifizieren. Im Rahmen des Projekts werden die OCT-Methode und die Hardware zur Messdatenerfassung für die Anwendung in der Inline-Qualitätskontrolle von Siegelnähten weiterentwickelt und ein Demonstratorsystem in eine Verpackungsmaschine integriert, um eine Validierung des Systems unter praxisnahen Bedingungen durchzuführen und die Anwendbarkeit des Systems im Produktionsbetrieb sicherzustellen.
Qualitätssicherung, Ressourceneffizienz und Basis für adaptive Siegelprozesse
Durch den Einsatz des Inline-Prüfgerätes können produzierende Unternehmen eine zeitnahe, komplett durchgängige Prüfung ihrer gesiegelten Folienverpackungen und somit deren Qualitätssicherung gewährleisten, ohne die Maschinenausbringung einzuschränken. Das Prüfsystem trägt so dazu bei, die Produktsicherheit für die Verbraucher zu erhöhen und die Prozesseffizienz zu steigern. Gleichzeitig werden durch die Möglichkeit, fehlerhafte Verpackungen bereits im Verpackungsprozess zu detektieren und das Packgut mittels Neuverpackung in den dem Prozess zurückzuführen, signifikant Ressourcen eingespart.
Neben dem unmittelbaren Nutzen für den Verpackungsprozess, ist das System ein wertvolles Instrument zur Erhöhung der Automatisierung des Verpackungsprozesses. Es ermöglicht die Prozessdatenerfassung und Schaffung interner prozessspezifischer Datenbanken für die Prozessanalyse. Damit schafft es die Grundlage für die Entwicklung adaptiver Siegelprozesse durch eine zeitnahe Fehlerdetektion und eine intelligente Anpassung der Prozessparameter im Siegelprozess.
Haben Sie Fragen oder wünschen Sie weitere Informationen zu unserem Forschungsprojekt? Wenden Sie sich gerne an uns!
Weitere Projektinformationen
Projektlaufzeit | 1. Juli 2022 bis 30. Juni 2025 |
Kooperatiosnpartner | Fraunhofer Institut für Keramische Technologien und Systeme IKTS, Kallfass Verpackungsmaschinen GmbH, IMM electronics GmbH |
Förderkennzeichen: | 13N16375 |
Projektträger /Zuwendungsgeber: |
VDI Technologiezentrum GmbH / Bundesministerium für Forschung, Technologie und Raumfahrt |