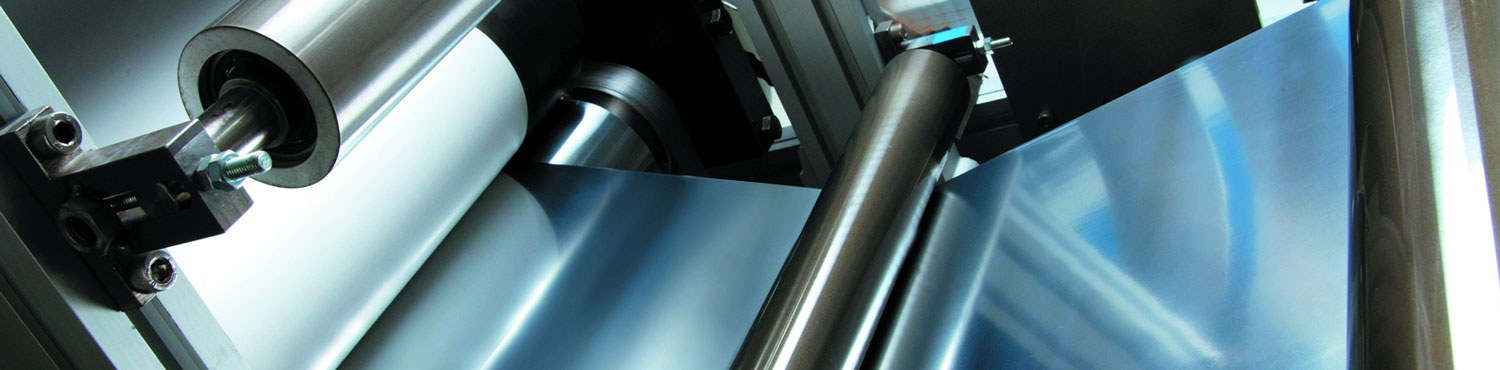
The lacquering and laminating plant enables us to bridge the gap between laboratory scale and production scale in the area of surface coating and multilayer manufacture. This small pilot scale plant offers you the opportunity to test combinations of materials before the production phase, to test application methods, to determine optimum process parameters, and to manufacture samples for application trials. A special film guide prevents contact between the functional layer and rollers after the coating process. This means that the plant is suitable for processing particularly sensitive high-barrier films coated on one side with thin layers.
The applications range from packaging films through to ultra-barrier films for the display market. The lacquering and and laminating of several layers enable materials with high barriers and functionalities such as heat resistance, moisture resistance, scratch resistance, and UV filtering to be manufactured.
The use of our lacquering and laminating plant for trials incurs significantly lower costs for you than when using your own production equipment.
The lacquering and laminating plant can be used with both low and high viscosity coating materials and can produce a wide range of layer thicknesses. Closed layers down to a thickness of 0.5 to 1 µm can be manufactured. To produce functionalized barrier films we can use nanocoatings or use combinations of vacuum coating and wet chemical processes. For the highest barrier requirements measures must be taken to ensure the film is dust-free. Such measures include the use of a clean air housing and web cleaning prior to lacquer application. Another key point is to avoid contact between the coated side and the guide rollers because this can damage or destroy the sensitive layer. The plant is suitable for the pilot production of ultra-barrier films up to a running length of 400 m (in combination with internally or externally manufactured inorganic layers). It is also possible to apply very viscous coatings such as starch solutions and adhesives. In addition to barrier properties it is often desired for films to have other functionalities. In many cases these can be introduced by using nanocoatings or specially cured lacquers. The processing expertise in this area has been successfully acquired by the Fraunhofer IVV during its participation in many publicly funded projects.