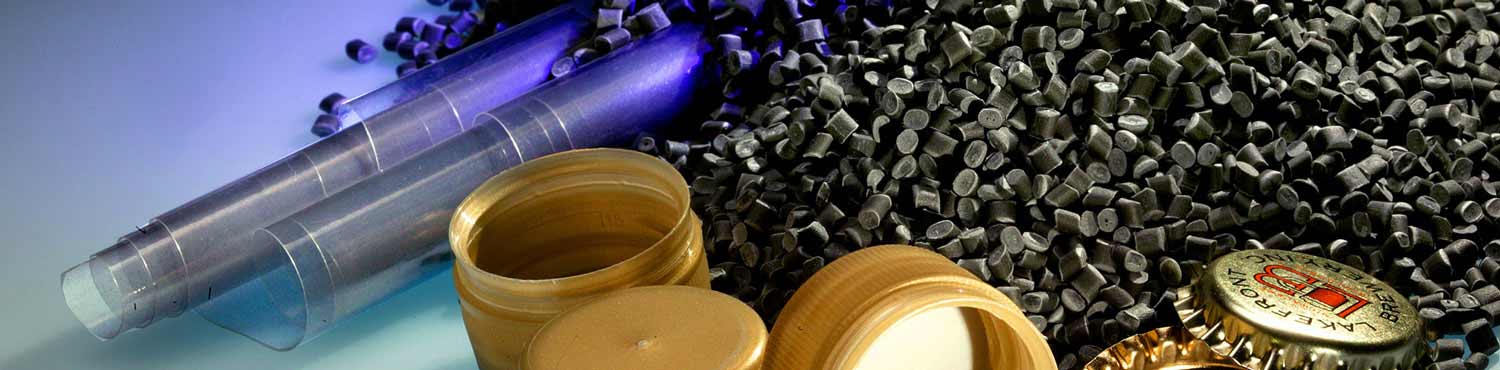
Our solvent-based process allows efficient separation of plastic composites and contaminated post-consumer waste. Odorous substances and contaminants (PBDE, HBCD, etc.) can therefore be efficiently removed. In order to recover high-purity materials from complex mixtures of waste materials, we specifically combine this method with mechanical, chemical and thermal processes.
For economic and technical process evaluation, we carry out trial runs producing high-quality polymer recyclates for you.
Our solvent-based process effectively removes contaminants and additives that reduce the quality of the recycled plastic produced by conventional recycling processes. This means that a wide variety of very pure plastics can be recovered even if they are initially present in mixed plastic waste. The high quality of the recycled plastics enables their reutilization to manufacture plastic products.
Dissolve | The target polymer is selectively dissolved in a special solvent formulation. Only solvents that are non-hazardous for users and the environment and that are certified in accordance with GHS criteria (Globally Harmonized System) are used. The specific solubility of the polymers allows their recovery with high purity. The non-hazardous solvents have high flash points and guarantee safe plant operation. |
Clean | Undissolved components are mechanically removed. Dissolved substances (e.g. non-target polymers, printing inks, aluminum oxide, odorants, hazardous substances) are removed at the molecular level using special purification steps. After the purification, one has a solution of macromolecules of the target polymer. The size and molecular weight distribution of these macromolecules are the same as in virgin materials. |
Precipitate | The target polymer is recovered from the solvent by precipitation. |
Dry | The recycled polymer is dried. |
Solvent treatment |
Distillation of the solvent recovered from the purification, drying, precipitation, and drying steps and its return to the recycling process. |
Product | The plastic recyclate is of high quality and can be used as a secondary raw material for the production cycle. |
The exceptional potential of the solvent-based recycling process stems from selective separation, allowing the recovery of pure polymers from complex mixtures of plastics. The target plastic is effectively separated from other materials such as metal, wood, and undissolved polymers. Mixed plastic waste and composite plastic materials such as laminated films, and shredder materials from the scrapping of end-of-life vehicles and waste electronic and electrical equipment which up until now have had to be disposed of via thermal energy recovery, landfill, or export can now be sustainably recycled. The recyclates from composite plastics and mixed plastic waste are of near virgin quality and for a circular economy can be returned to production processes. Special purification modules also allow the separation of undesired low molecular weight materials. Our solvent-based recycling process therefore for the first time allows the closed-loop recycling of contaminated plastic waste such as building waste containing polystyrene mixed with flame retardants.
Compared to mechanical separation methods, solvent-based plastic recycling has the advantage that the target polymer is selectively dissolved and as such is recovered with high purity. Other polymers and other solids remain undissolved and can be effectively removed. Dissolved contaminants such as flame retardants and plasticizers are separated using specific solvents, allowing the recovery of high-purity plastic recyclates. Waste fractions that cannot be recycled using conventional recycling processes are thus made available for a circular economy.
Publication for download: