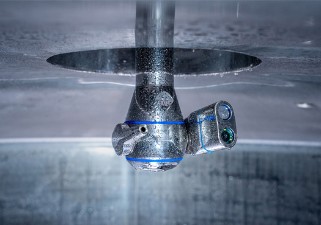
At drinktec 2025, the Fraunhofer Institute for Process Engineering and Packaging IVV will present three technology solutions that use AI, powerful software and newly developed contamination sensors to eliminate the problem of safety-related, systematic oversizing of cleaning processes in hygiene-critical areas such as heat exchangers, tanks, and pipelines. The key to this is knowing when, where, and how much contamination is present and, based on this information, carrying out a precisely tailored cleaning process.
more info