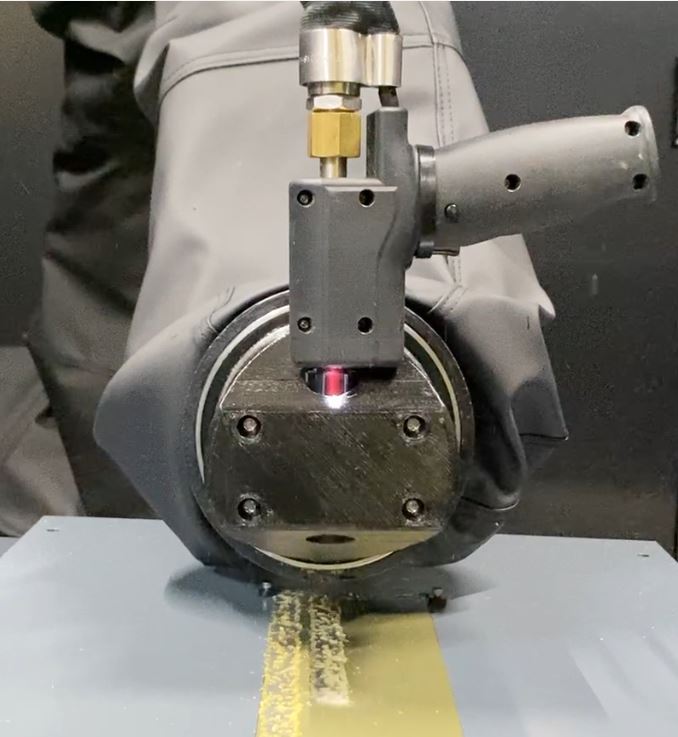
Dry ice cleaning - sustainable, gentle and effective
In view of the increasing demands for sustainability, resource efficiency and flexibility in cleaning processes, dry ice cleaning offers an environmentally friendly and efficient solution, even for areas that are difficult to access.
In this process, solid, deep-frozen carbon dioxide (dry ice pellets) is shot onto the surfaces to be cleaned using compressed air. The dry ice creates a mechanical effect on impact and loosens the dirt from the surface. As the low temperatures embrittle the layer of dirt before the impact, it is easier to remove from the surface.
In addition to the good cleaning effect, a decisive advantage lies in the sublimation of the dry ice: it changes directly from a solid to a gaseous state without melting. This means that there are no residues of the cleaning agent and no waste water. The elimination of drying times also means that the cleaned surfaces can be used again immediately. Dry ice is non-abrasive if the parameter configuration is adapted to the surfaces. The cleaning process is therefore very gentle on materials, even on sensitive surfaces.
Fully adaptive automation solution with innovative inline contamination sensor technology
Until now, dry ice cleaning has mainly been used for niche applications and has only a very low level of automation. In order to make the advantages of the process available for broad industrial use, we are developing a fully automated, adaptive dry ice cleaning system as part of the research project.
The movement path of the cleaning robot is planned automatically. The basis for this is the component geometry and the information on the locally varying degree of soiling of the component determined using intelligent UV-VIS sensor technology. The innovative inline sensor detects both filmic and particulate contamination.
The optimum choice of parameters, in particular the pressure and the appropriate granulate size, is crucial for the success of the cleaning process. With the help of AI, the soiling status before and after cleaning as well as the type of soil are determined from the sensor data and the optimum parameters for the cleaning process are derived from this. The innovative sensor technology also enables automatic documentation of the cleaning results.
Detection of contamination type and condition using AI
The contamination detection technology is based on a camera with UV light. This sensor localizes the dirt on the cleaning object and uses AI to plan the optimum cleaning process.
By creating a virtual twin of the component, the images captured by the camera can be mapped or assigned to the surface model of the object. This creates a "soil map" that shows where the dirt spots are located in the room. To ensure efficient and thorough cleaning, the cleaning process can be dynamically adapted using this map.
The virtual twin also makes it possible to accurately map the real dirt digitally and to control the cleaning process in a targeted manner through the use of AI. Two AIs are being "trained" in the project: An AI for detecting soil and an AI for developing efficient cleaning strategies. These will be developed and continuously refined based on the expertise at the Fraunhofer IVV and intensive cleaning tests.
By constantly learning and adapting to new data and findings, the efficiency and accuracy of the AIs can be continuously improved.
The combination of digital representation, virtual twins and on-demand learning using AI technology enables precise and efficient cleaning of contaminants and continuous improvement of cleaning processes..
Project information
Cooperation partners: |
Mess-, Prüf- und Handling-Systeme GmbH (MPH Automation), HaDo International GmbH |
Project sponsor/Grant authority: | Bundesministerium für Wirtschaft und Klimaschutz BMWK aufgrund eines Beschlusses des Deutschen Bundestages |
Funding reference: | KK5047707CM3 |