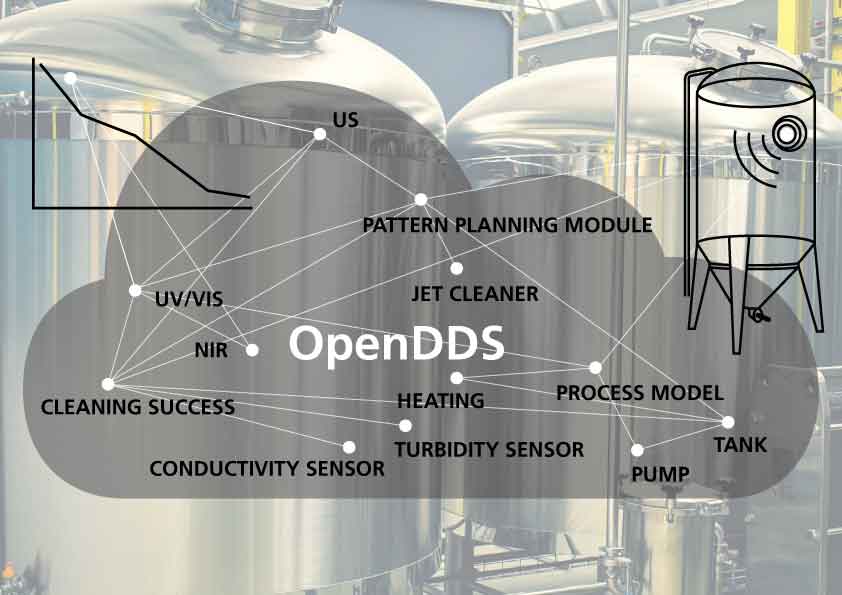
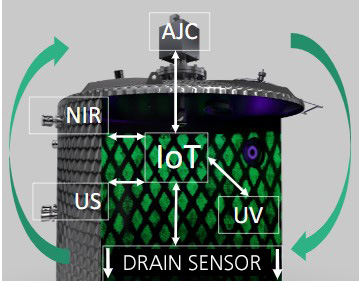
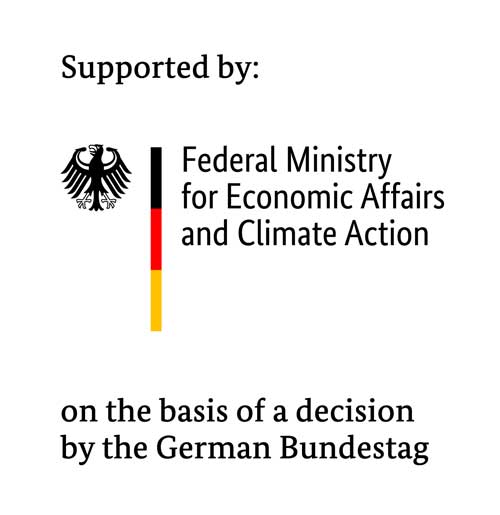
CIP tank cleaning customized for the product rather than a “worst case” approach
Building on our Adaptive Tank Cleaning project and following a new paradigm, we are now focusing on ways to significantly reduce excess cleaning processes in the beverage and food industry. Our research analyses have found that 60 % to 90 % of the time spent for tank cleaning is not utilized in a need-based way. This occurs because, to meet the required hygienic and quality standards, the cleaning process is commonly designed based on the assumption of the worst case of contamination. Consequently, cleaning is performed using far more resources than are required for the real contamination situation.
In the preceding project focusing on adaptive CIP tank cleaning, the team has already succeeded in implementing a tank cleaning process that very closely estimated real cleaning needs: By means of an intelligent, self-learning cleaning system with optical Inline contamination detection sensors, up to 35 % less water was consumed, while energy use was reduced by more than 50 %.
Now the researchers intend to further optimize these saving potentials: Their goal is to reduce up to 75 % of the energy and 50 % of the time needed for cleaning in comparison with benchmarks. For this purpose, they have engineered an agent-based approach with the Internet of Things (IoT).
IoT agents negotiate the optimal cleaning strategy
The approach starts with designing an innovative complex smart sensor system combining various sensors, such as ultraviolet, near infrared, ultrasound and drain sensors. This system is then implemented in “cleaning agents” involved in the cleaning process, such as the Adaptive Jet Cleaner, the pump, the heating device, and the tank.
Once equipped with a smart functionality, these agents can not only transfer data related to the cleaning parameters, but also actively communicate to determine a cleaning strategy tailored to the specific contamination situation. For this purpose, in the next step, an openDDS IoT system must be engineered to connect the agents wirelessly.
Introducing both trajectory planning and Inline optimization modules, the team can extend the system by two agents capable of customizing the cleaning process to make it more specific to the needs of the users.
Are you still cleaning or already producing?
A cleaning process customized to the product makes cleaning time shorter. Shorter cleaning processes, in turn, increase equipment availability and thus efficiency. Moreover, it is possible to manufacture new products without investing in new equipment.
Another advantage is offered by the new Inline optimization tool. It makes it possible to individually customize the process to adapt to ever-changing user requirements. If, for instance, cleaning must be done very quickly, since order performance is time-critical, then the agents can implement this just as well as managing a cleaning process that specifically minimizes resource use but is less time-sensitive. It is also possible to appropriately balance the individual objectives.
Applying product-adapted cleaning processes also increases process efficiency, because energy, water, and the consumption of cleaning agents can be significantly reduced. This benefits the operating result and protects resources and thus our environment.
The working model of an OpenDDS-controlled intelligent CIP tank cleaning design research project in the Hygienic Production research division at the Fraunhofer IVV in Dresden.
Futher Project Information
Project term: |
November 1, 2020 to April 30, 2023 |
Project partner: |
University Erlangen-Nuernberg, Department of Chemical and Biological Engineering, Chair of Fluid Mechanics |
Project management/funding |
German Federation of Industrial Research Associations AiF (through the Research Association of the German Food Industry FEI / Federal Ministry for Economic Affairs and Climate Action BMWK) |