Utilizing the benefits of additive manufacturing processes for systems in food and pharmaceutical industries
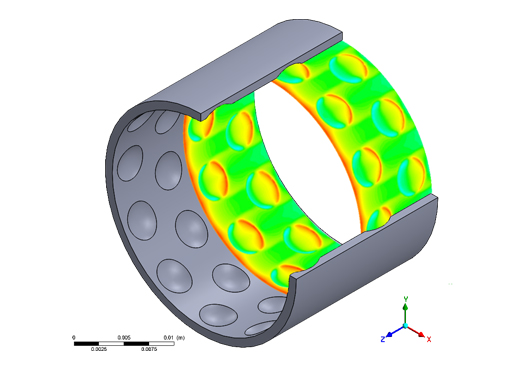

3D printing processes can produce complex shapes without tools, which either cannot be produced conventionally or can only be produced with a great deal of difficulty, thus making them the ideal solution for custom manufacturing. Although this is a process technology of the future, it also poses certain challenges with regard to its use in hygiene-critical areas.
In metallic 3D printing, e.g. laser beam melting, the produced surfaces do not possess the necessary hygienic surface characteristics to be able to guarantee and maintain the safety and quality of the products due to their high degree of roughness.
The »HygAM« research project focuses on developing solutions that improve these surface characteristics to meet specific requirements so that metallic 3D printing is suitable for hygienic applications in food and pharmaceutical industry systems.
Optimization of 3D printing parameters to reduce surface roughness
The printing process exposure strategy was adjusted in order to improve the overall surface evenness and as a result also improve the output surface quality during the 3D printing process. This involved analyzing and evaluating crucial process parameters such as laser power, scanning speed and the critical angle. As a result, not only could the surface porosity be kept to a minimum, but peak roughness could also be reduced by around 60 %.
Inspired by a golf ball: Improved cleanability thanks to targeted flow control
Macrostructures on surfaces (like dimples on a golf ball, protrusions or spiral structures) make it possible to generate targeted flow vortices. This can be used to enhance heat and mass transfer processes. The »HygAM« project researched how this concept can improve the cleanability of surfaces.
3D flow simulations were used to investigate the cleaning properties of various macrostructures, after which the geometry of the two most promising structures (dimples and protrusions) was optimized based on the simulations.
Subsequent cleaning tests revealed that the components with macrostructured surfaces were less prone to microbial contamination than an additively manufactured reference component without macrostructures.
Combination with specific surface finishing procedures to achieve the required cleanability
Additional surface finishing of the components is necessary in order to achieve a level of cleanability comparable to that achieved by conventionally manufactured components. The internal surfaces of closed geometries are either only partially accessible or completely inaccessible to conventional surface finishing technologies. In these cases, specific processes such as hirtization, flow machining and electropolishing are required. The project analyzed the potential uses and limitations of each of these processes and confirmed their validity through subsequent cleaning tests.
The results confirmed that additively manufactured straight components with optimized macrostructuring and subsequent surface finishing by means of flow machining produced cleaning results that were identical to those of a conventionally manufactured reference pipe.
Additional project information HygAM
The IGF project 20790 BR of the Industry Association for Food Technology and Packaging e. V. (IVLV e.V.) research association is funded by the German Federal Ministry for Economic Affairs and Climate Action (BMWK), via the German Federation of Industrial Research Associations (AiF) within the framework of the program for promoting collective industrial research (IGF) on the basis of a resolution of the German Bundestag.
Project duration | Sept. 1, 2019 – Feb. 28, 2022 |
Project partners: | Fraunhofer IWU |
Project sponsor/grant authority: | Arbeitsgemeinschaft industrieller Forschung AiF (via Industrievereinigung für Lebensmitteltechnologie und Verpackung e. V. — IVLV) / German Federal Ministry for Economic Affairs and Climate Action (BMWK) |
Additional project information HygAM 2
Project duration: | March 1, 2023 to February 28, 2025 |
Project partner: | Fraunhofer IWU |
Funding code: | 22680 BR |
Project sponsor/grant authority: | DLR Projektträger (via Industrievereinigung für Lebensmitteltechnologie und Verpackung e. V. — IVLV) / German Federal Ministry for Economic Affairs and Climate Action (BMWK) |