High Protein = High Cleaning Effort?
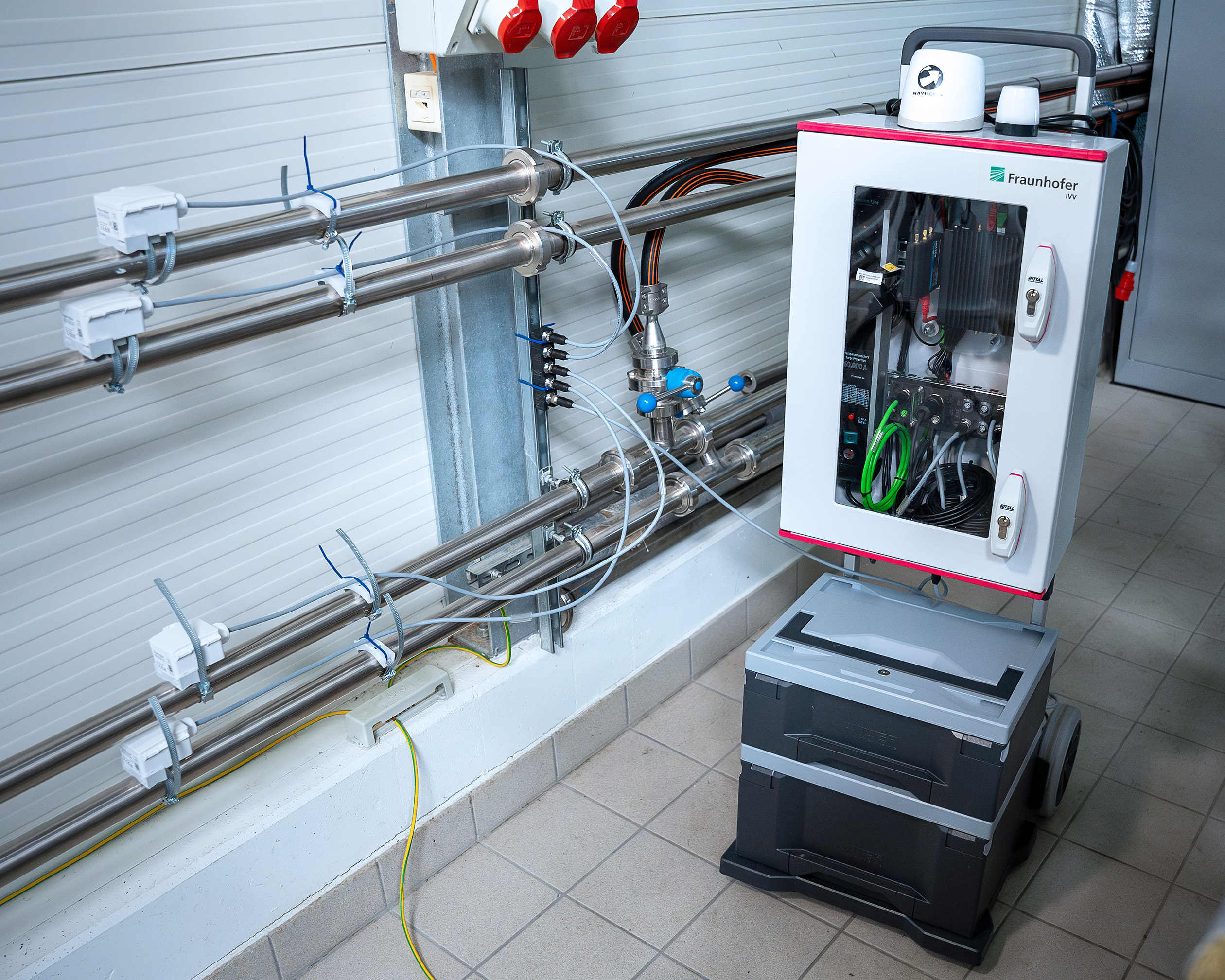
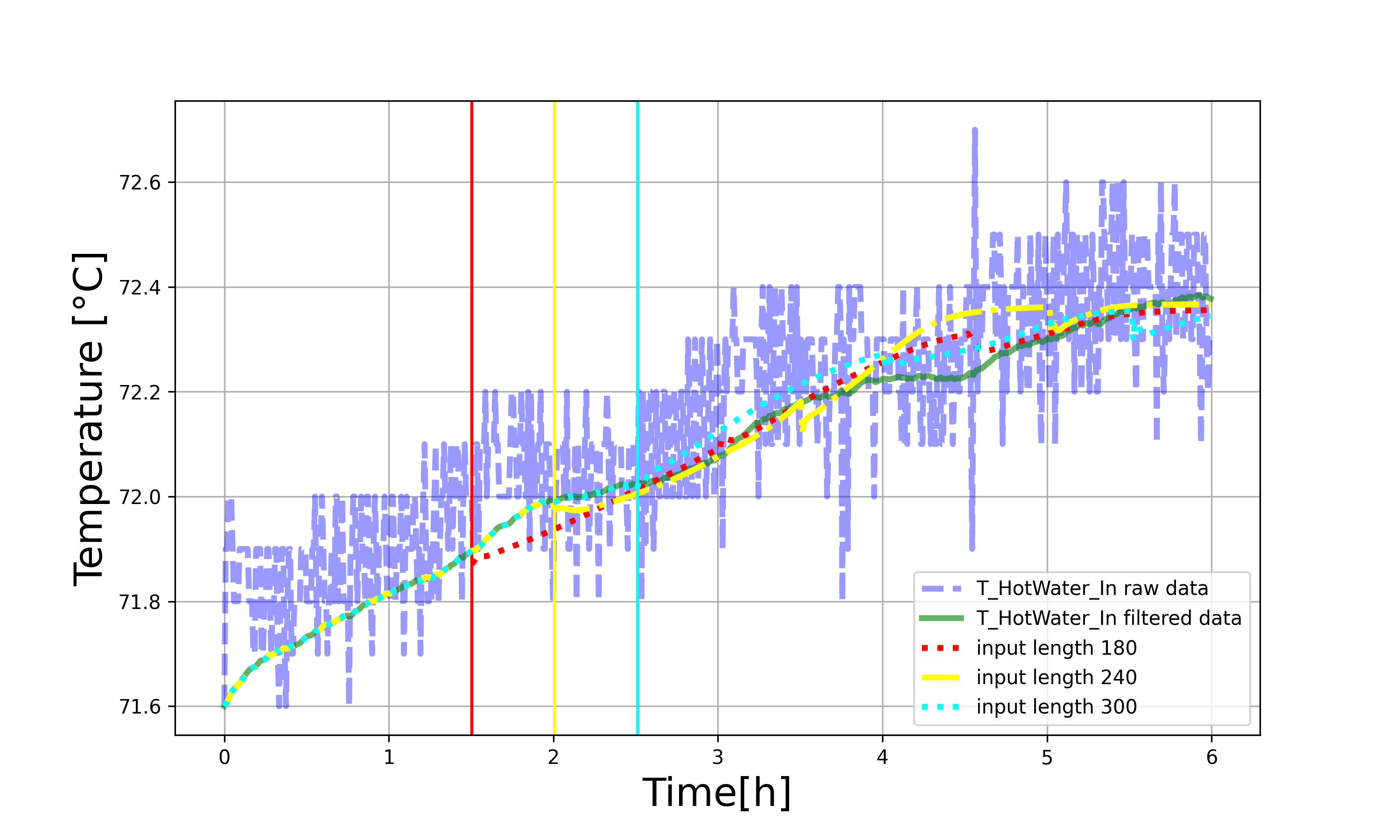
More protein, more effort
In industrial dairy processing, processes such as pasteurization and ultra-high temperature treatment are essential for ensuring product safety and extending shelf life - at the same time, there is growing pressure to use energy and resources more efficiently.
A key problem here is fouling, i.e. the build-up of proteins, fats and minerals on the surfaces of heat exchangers. This impairs heat transfer, impedes the flow and jeopardizes process reliability. The result is frequent cleaning, long periods of downtime, and high water, energy and cleaning agent consumption.
High-protein products such as yoghurt drinks and mixed milk drinks, which are currently in high demand, present a particular challenge. Their high protein content significantly increases deposition tendencies, making process control more difficult and increasing operating costs and increases the risk of microbiological contamination.
Smart prediction makes the difference
In order to address these challenges, the Fraunhofer IVV and the TU Braunschweig have entered into a collaborative research partnership named »Fidelio«. This project aims to develop an AI-based monitoring system that can detect fouling in heat exchangers during the heating process.
The new »CoControl-FouliQ« sensor uses real-time data from four clamp-on temperature sensors at the inlet and outlet of the heat exchanger, which is evaluated by a machine learning model that has been specially trained for this purpose. Temperature curves serve as an indicator for incipient deposits, enabling efficient planning of cleaning operationsin accordance with demand, as opposed to fixed intervals.
Ready for implementation
The »CoControl-FouliQ« system consists of temperature sensors, a compact control cabinet computer unit and a machine learning model for data evaluation and fouling prediction. The system's clamp-on temperature sensors allow for seamless integration with existing infrastructure, minimising the effort required for implementation. The innovative hardware solution has been developed for use in demanding production environments of dairies.
»CoControl-FouliQ« was tested over several weeks in a real-worl-setting within a dairy plant. The results demonstrated the system's capability to accurately predict fouling occurrences The model demonstrated high stability and accuracy, particularly with longer data series.
The implementation of on-demand cleaning measures has been shown to result in a significant reduction in the number of cleaning cycles required in the ultra-high-temperature process (UHT). The validation confirms »CoControl-FouliQ« as a solid basis for predictive maintenance and process optimization in milk heating. This can result in reduced consumption of resources, minimised downtime and enhanced process stability, particularly for high-protein products.
Conclusion:Predictive detection of fouling - Enhancing safety and efficiency
With »CoControl-FouliQ«, dairy plants can benefit from AI-powered fouling detection, which is both reliable and provided at an early stage in the heating process. By scheduling cleaning operations according to demand, the system contributes to resources conservation and optimized plant availability, while also enhancing product safety through the assurance of consistent and reliable process control. »CoControl-FouliQ« is designed to ensure more stable processes, fewer periods of downtime and more sustainable production, especially for demanding high-protein products.
Further project information
Project duration | February 1, 2022 – August 31, 2024 |
Project partner | TU Braunschweig |
Project sponsor/Grant authority: | Deutsche Bundesstiftung Umwelt |