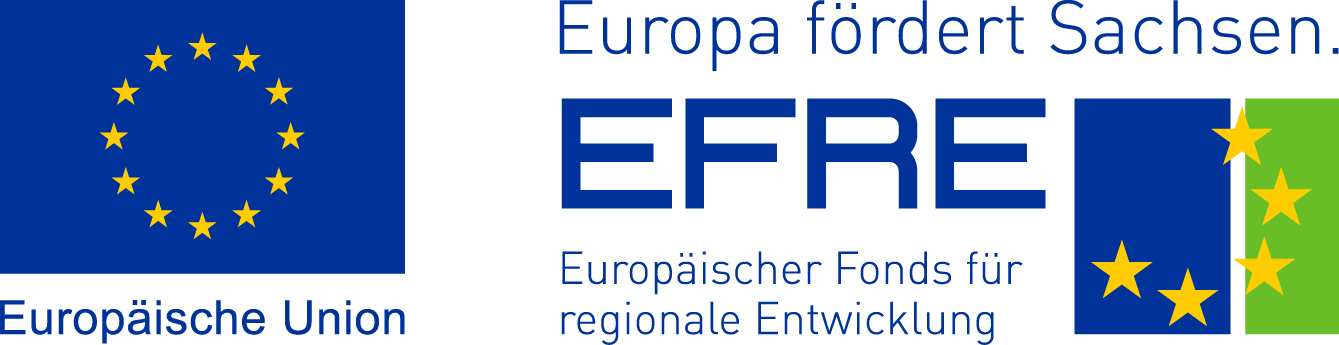
Image-Processing Methods for Disturbance Detection
Within the opticSAM project, a software for recognizing disturbances on processing and packaging machines and installations is being developed. By using image-processing methods, the possibilities for disturbance detection are significantly extended, compared to sensor-data-based approaches. The system for optical disturbance detection is connected to an assistance system for machine operators, acting as a central platform, which does not interfere with the production process, but only supports the machine operator.
Efficiency Increase by Optical Methods for Disturbance Diagnosis
The technical efficiencies of processing and packaging machines and installations can exceed 95 %. However, in day-to-day production, a large number of micro-disturbances (< 2 min) significantly reduce the actual efficiency. These recurring downtimes result in high scrap rates, waste of resources and the aforementioned reduced production efficiency.
In order to minimize the number and duration of disturbances and thus increase production efficiency as well as reduce scrap quantities and waste of resources, various approaches can be considered. One possibility is the support of machine operators in diagnosing and eliminating disturbances. Disturbances in processing and packaging machines and installations are typically characterized by long cause-effect chains, requiring expert knowledge to diagnose, which is not available to all machine operators. As a result, the cause of the disturbance is often not eliminated sustainably.
The self-learning operator assistance system SAM adopts this approach and provides machine operators with a software that helps them eliminate disturbances. Within the opticSAM project, machine image data is recorded by camera and then analyzed using machine learning algorithms in order to detect disturbances and extract valuable information for machine operators. Particularly for machines and installations with few to no sensors, this allows extensive evaluation without the need for retrofitting a large number of sensors. An integration into the machine control is thus not necessary.
Practical Research - Industrial Application
Developing optical disturbance recognition, Fraunhofer IVV Dresden relies on the cooperation with industry partners in order to take requests, ideas and concerns into account at an early design stage.
Initially, the system will be implemented and tested in laboratory scale with a demonstrator at the Fraunhofer IVV Dresden. It will then be installed on-site at interested partners and evaluated under field conditions. Several industry partners have already joined research.
If you are interested in our project, do not hesitate to contact us!
Further Project Information
Project term: | 2019 to 2020 |
Project management /project funding: |
Sächsische Aufbaubank /State of Saxony |