Forming air impact technology
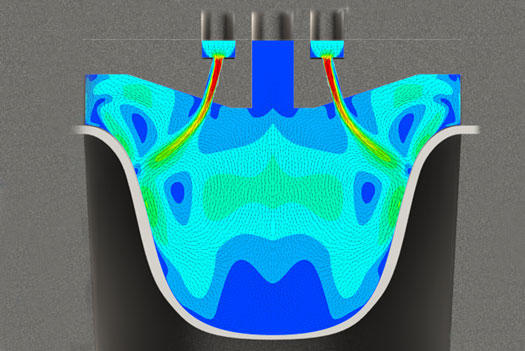
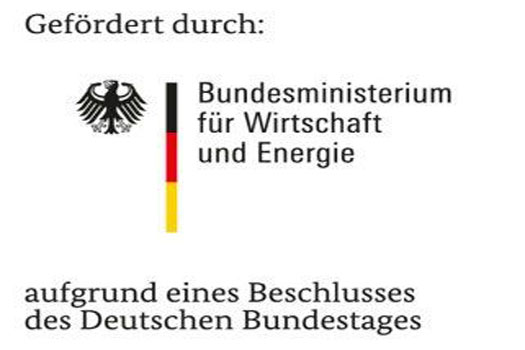
Thermoformed components often have widely varying material thickness
Thermoforming is an efficient process for manufacturing packaging systems, consumer products, and components for, for example, the aviation and automotive industries. A key quality criterion is the mechanical stability of the formed component and this largely defines the required material usage. Up to 80% of the cost of a formed component is the material cost. This is due to the high amount of material needed for homogeneous heating of the film of variable thickness in the thermoforming process. A research project being conducted by Fraunhofer IVV aims to minimize material usage and improve the mechanical stability. The material thickness distribution is controlled in a defined way by local use of forming air in the thermoforming process. This new technology has considerable economic and ecological benefits.
Improved thickness distribution in thermoformed components via directed local air flow
One approach being pursued is to use a local air flow directed onto the film (forming air impact) to improve the material thickness distribution across the product. By having controlled material thickness, the total material usage can be reduced. The objective of the project is to evaluate the economic and technical potential of this approach. Due to the many parameters involved (e.g. nozzle diameter/distance/angle), a key intermediate objective is to weight the importance of these parameters. This is a prerequisite for effective dimensioning of the technology for transfer to specific industrial applications.
The Fraunhofer IVV Dresden is developing a tool for application of the forming air onto the polymer film. Furthermore, a structural-mechanical thermoforming model is being developed, a material model is being selected, and packaging material specific parameters for this are being determined. These models form the basis for a fluid-structure interaction model being developed in collaboration with the Friedrich-Alexander Universität Erlangen-Nürnberg. This will allow effective analysis of the fluid properties on the forming behavior of the polymer and hence weighting of the design and process parameters. Finally the Fraunhofer IVV Dresden will assess the potential of forming air impact on a product of commercial relevance.
At the end of the project there will be an efficient and economically viable technology for significantly improving the product quality, material thickness distribution, and resistance to compression. The technology will also help lower the material usage for manufacturing molded plastic components.
Further Project Information
Project term: | 2016 to 2018 |
Project management /project funding: |
Federation of Industrial Research Associations AiF (via the Industrievereinigung für Lebensmitteltechnologie und Verpackung e. V. (IVLV)) /Federal Ministry for Economic Affairs and Energy (BMWi) |